HABSHAN 5 IGD
PROJECT Habshan 5, one of the world's largest gas treatment plants, was developed to boost UAE's gas production. Tecnimont, in a joint venture with JGC, secured a landmark EPC contract from ADNOC Gas Processing.Gas treatment capacity
Peak presence at site
Safe man-hours without LTI
Habshan 5 is one of the largest gas treatment plants worldwide and has been developed to accommodate additional Offshore Gas production and additional associated gases that will become available as a result of the expansion of ADCO's onshore oil production.
In July 2009 Tecnimont, in a 50%/50% Joint Venture with JGC of Japan, was awarded one of the largest EPC LSTK contracts ever tendered in Abu Dhabi in the Oil and Gas sector by GASCO (now ADNOC Gas Processing), a major gas processing company worldwide.
The contract is part of the giant Integrated Gas Development (IGD) project being carried out by GASCO, a subsidiary of the state-owned hydrocarbons giant, Abu Dhabi National Oil Company (ADNOC), and responsible for the processing of natural gas and associated gas onshore in UAE.
The IGD project aimed to increase UAE offshore gas production from the Umm Shaif Khuff and Umm Shaif Area reservoirs by 1,000 mmscfd. The offshore gas, after initial treatment in the new Das lsland facilities, is sent through a dedicated 30-inch pipeline to the Habshan site in the southwest part of the Emirate, where it is further processed before going to the gas sales network. Recovered NGL is sent to the Ruwais site for further fractionation and export.
Work was completed by October 2013 upon execution of Test Runs of all process Units. thus helping meet the rapidly increasing demand for gas resources in the United Arab Emirates.
The project was carried out at several international locations - ltaly, Japan, India, Philippines, Pakistan and the United Arab Emirates - with detailed engineering and procurement managed by a first-class team of ltalian and Japanese managers.
The up-to-date technology used to connect the various operating centres in different time zones created a "virtual global office", in which more than 800 engineers worked, virtually on a 24/7 basis, towards a common goal. The combination of so many different cultures made the Habshan project a real melting-pot, in
which all personnel bring their individual backgrounds and experience to contribute.
A few comparisons illustrate the scale of the project: the steel structures in the Habshan process facilities will be sufficient to build more than seven Eiffel Towers; the length of the electric and instrument wiring in the plant is equal to around a fifth of the earth's circumference; and the quantity of concrete used in the project will be sufficient to build a copy of Kuala Lumpur's twin Petronas Towers, the world's fifth tallest buildings.
The Habshan 5 project is impressive also in terms of safety performances: it was reached the target of more than 100,000,000 man-hours without Lost-Time lnjury (LTI), according to the OSHA (Occupational Safety and Health Administration) standards.
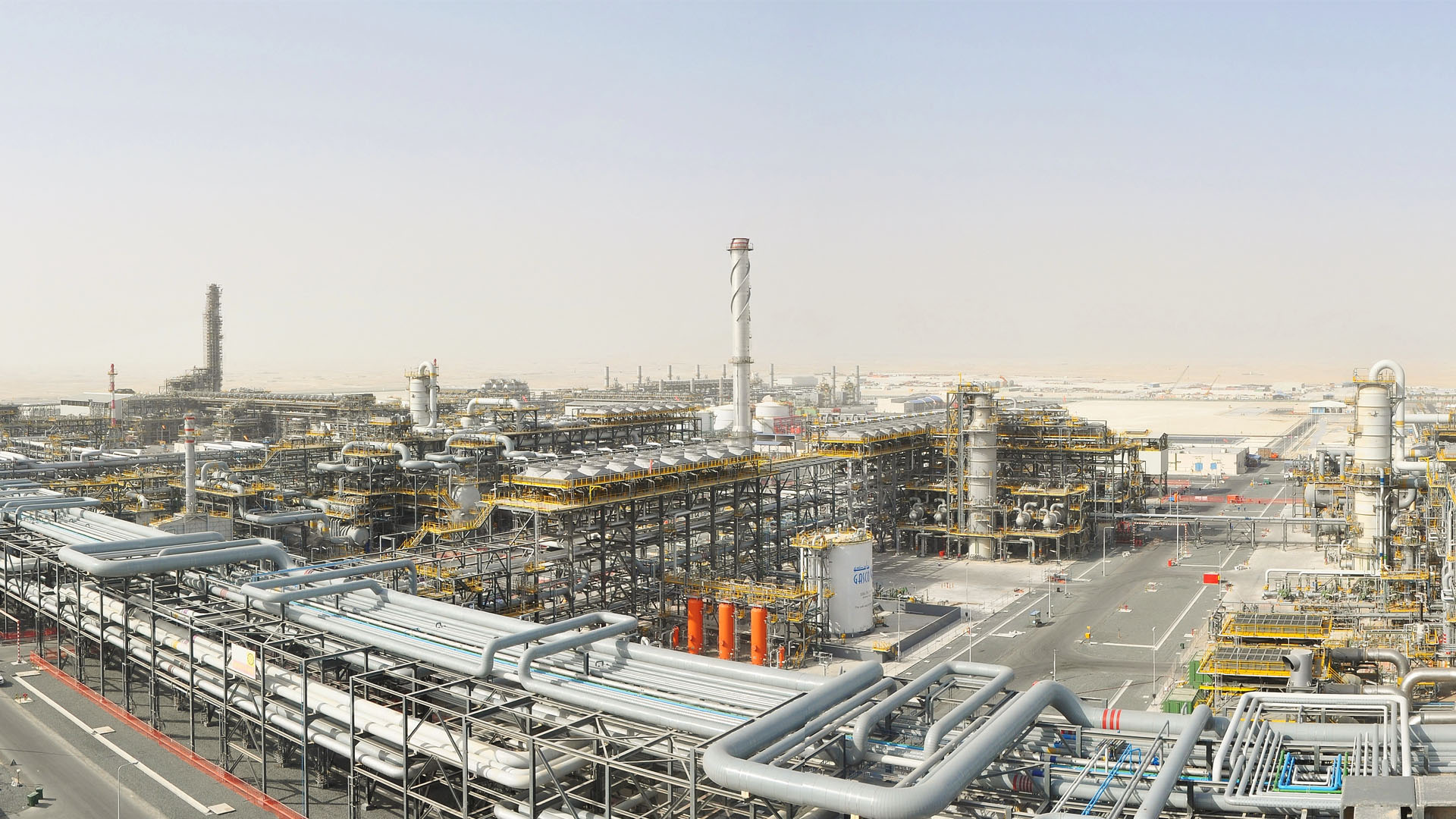
THE STEEL STRUCTURES IN THE HABSHAN PROCESS FACILITIES WILL BE SUFFICIENT TO BUILD MORE THAN SEVEN EIFFEL TOWERS
DISCOVER OTHER PROJECTS
Get to know us and how we work by browsing through our current and past projects.